Bund Lining Systems: The Alternative Resin Types
Bund Lining systems can be produced from several different synthetic resin technologies that are predominantly reaction hardening, which means they harden or set into a solid lining material on the surface of the area you are protecting, as the result of mixing their two or more components together and applying the liquid mixed product at the specified thickness. This mixing is obviously a critical step that must be done correctly to ensure that a fully homogeneous product is applied. It is therefore usually done with special low speed mechanical mixing equipment and in in each individual products defined mix ratio.
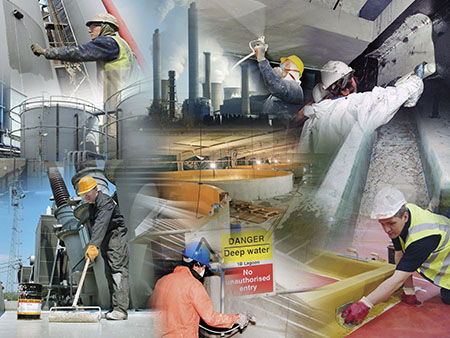
Generally resin lining and protective coating products are supplied pre-batched in the right proportions to be mixed together, although on larger projects some contractors with specialist equipment, can handle bulk supplies of the products component parts, which can significantly reduce costs and packaging waste. Mixing of 2-component synthetic resins must always be done thoroughly and for a defined period of time, shortly before application and sometimes, with spray applied resin coating systems, the two-components are actually mixed together at the nozzle as they are being spray applied – usually the best solution for fast and very fast curring and setting resins such as 2-component VIP Quickcoat Polyurea resin based protective coating and lining systems.
One-Component Bund Lining Materials
One / single component resin materials are not generally suitable for use in industrial and commercial facilities for their Bund Lining applications as these are usually exposed and / or trafficked. This is due to their lower inherent mechanical strengths and chemical resistance, which means tha they will not be sufficiently resistant and durable in these situations.
However there are one component Bund Lining Materials that can be more than adequate for domestic or limited commercial applications with limited exposure and traffice, where their properties are therefore adequate – for example in domestic fuel oil storage tank areas.
For these straightforward external applications NCC Bund Lining experts tend to propose the use of Sikafloor®-400 N Elastic, which is a one part, easy to apply, highly elastic, solvent containing, crack-bridging, waterproof and UV resistant, coloured, moisture curing polyurethane resin based protective coating that is fully resistant to domestic oil and sewage, plus many other dilute chemicals.
Sikafloor®-400 N Elastic has also been tested and certified as a resistant top coat in the “Ground Water Protection System”, according to German Standards Z-59.12-4, DIBt, dated June 2003.
Despite the relatively good performance from this one / single component resin product in particular, on almost every industrial and commercial project we prefer to recommend the use of higher performance two-component resin based lining and protective coating systems as increased security for our contracting customers and their clients. However if the areas future exposure is strictly limited and controlled, then the use of the relatively low-cost, one-component Sikafloor®-400 N Elastic lining system can always be considered.
Two-Component Bund Lining Materials
The most commonly and widely used Bund Lining material technologies used in the UK are two-component resin based systems. These include 2-part epoxy resin coating systems, 2-part polyurethane resin coating systems, 2-part vinyl ester resin systems and 2-part polyurea resin systems.
All of these different ‘2-part’synthetic resin Bund Lining systems, or ‘2-component’ Bund Lining materials as they are more correctly known, are generally all supplied to site as separate units that are pre-batched in the correct proportions, which are known as the products ‘mixing ratio’.Alternatively for large projects and contractors with the necessary specialist equipment, each individual component can be supplied to site in bulk containers. This means that the components must be correctly measured and dosed on site following strict Quality Control procedures and as much of the process automated as possible to reduce the risk of human error.
The two components of these systems are generally referred to as the ‘resin base’ and the ‘resin hardener’ or ‘resin catalyst’, whichare then required to be thoroughly mixed together.
Technical note: the second component is the ‘resin hardener’ if it takes part in the reaction and forms part of the structures of the cured and hardened resin product; whilst it is a’resin catalyst’ if the material simply triggers or accelerates the hardening reaction, but does not physically take part in it or change and is therefore still there in the same form at the end. Basically in these instances, the reaction tends to start because it is physically accelerated on the surface of the catalyst, which is also why 2-component resin catalysts are generally in the form of powder, because the use of fine particles means the material has the largest possible surface area for this initial acceleration to take place and start the reaction throughout all of the mixed material. In both cases with a hardener and a catylst there is often associated heat generated (the reactions are exothermic) and this will also accelerate the reaction and so this must be controlled by only mixing sufficient volumes that can be used immediately for example.
The mixed resin lining / coating material is then applied onto the prepared concrete substrate and this must be undertaken and completed within the products defined ‘pot-life’. This means its ‘working time’ or ‘useable time’ which is normally defined at given ambient and substrate temperatures and humidities, before it has become too thick or otherwise is unworkable or otherwise over this limit and so can no longer be applied. There is a useful old 'rule-of-thumb' that has been used on site over the years by experienced resin specialists, which says that: "an increase of 10°C will roughly halve a product’s pot-life, whilst a drop of 10°C will roughly double the pot-life" – however the manufacturers specific recommendations and advice must always be ollowed for each individual product of course.
Technical Note: As a note of caution there are also some 2-component resin systems where this critical change is not easily or visably perceived, so extreme care should be taken i.e. with some water dispersed acrylic resin based injection and surface sealing solutions.
With reaction hardening resin products the two components begin to react with each other as soon as they start to be mixed together. Once mixed the product hardens to form a durable resin lining in it's defined hardening, or curing time as this is known, which is also normally defined and stated at given ambient and substrate temperatures and humidities. This reaction time is also referred to as the resin materials ‘hardening’ or ‘curing’ time and this is also generally reduced at higher temperatures and increased at lower temperatures – and the same rule of thumb from experienced resin specialists also generally applies to this i.e. an increase of 10°C will roughly halve the hardening time, whilst a drop of 10°C will roughly double the hardening time - (although always check and observe the specilialist product manufacturers stated limitations in the PDS).
The length of time before the area can be put into use will then vary according to the type of resin system, from immediately with some systems, to several days with others, which again will be temperature and humidity dependent. Additionally some two-component resin based bund lining and coating systems may require protection from the elements or exposure to water, chemicals or traffic for all or some of this period.
Typically the initial curing time for 2-component resins can be from 1 to 24 hours (although as little as a few minutes or even less with some special products mixed at the nozzle such as some of the VIP polyurea systems), with additional time possibly being required for the products full chemical and mechanical / abrasion resistance to be achieved, typically in from 1 to 7 days – again this is all dependent on the resin type, the specific product formulation, the application conditions and the intended exposure. A full understanding of the site, the environmental conditions, and the Bund Lining system product application and performance are therefore all essential for a successful and durable installation.
The Bund Lining specialists at NCC can always advise you on the most suitableBund Lining type and the best specific Bund Lining product(s) for your specific project needs. Please call any of our offices for specific assistance from our experts.
The following pages of generic information on the different types of resin Bund Lining materials technologies, is intended to provide you with an overview of the typical and characteristic properties of each of the different types of synthetic resin lining and protective coating materials – Although as we have already cautioned, almost by definition within any generic group there can be substantial and wide variations in the different products application and performance characteristics due to the range of resin chemistry formulation possibilities. However in the following pages of this website we will try to review and discuss each of these resin materials technologies in more detail, to help you to understand the alternative possibilities that are available, together with their main advantages and any limitations in relation to their use. Hopefully this will be of assistance in defining and selecting the best type of Bund Lining system for the protection of primary or secondary containment areas for your project.
If you would like any additional advice or assistance for your Bund Lining project then please call any of our offices and one of our experts will be delighted to assist you. NCC provide FREE independent and detailed advice and can supply the full range of the best performing Bund Lining technologies and protective coating systems that are available on the market today.